Circular Economy
Tyres are one of the most circular products on the market
The tyre industry is at the forefront of the circular economy, ensuring optimal resource efficiency and environmental performance. Tyres are designed for longevity, and their lifecycle is extended through retreading, recycling, and material recovery, contributing to waste reduction and resource efficiency.
ETRMA is a member of the European Commission’s Ecodesign Forum, which will play a pivotal role in implementing the new Ecodesign for Sustainable Products Regulation (ESPR). ESPR aims to establish circularity requirements for tyre design. To maximise its effectiveness, harmonised regulations are needed to prevent overlaps, particularly concerning remanufacturing and refurbishment.
Retreading – Maximising Resource Efficiency & Reducing Emissions
Retreading extends the life of tyres by replacing worn tread with new material, cutting waste generation and raw material consumption.
This process is an exemplary practice of the circular economy:
- A single tyre retreaded twice reduces 160 kg of waste and saves 104 kg of raw materials.
- Truck tyres are designed to be retreaded up to three times, significantly reducing CO2 emissions.
- The retreading sector supports 30,000 jobs across Europe, primarily in SMEs.
Management systems of End-of-Life Tyres
The European tyre industry has achieved a 95% ELT collection and treatment rate, transforming used tyres into secondary raw materials. These materials support industries such as construction, automotive, cement, and road infrastructure.
In 2021, 95% of ELTs in Europe were collected and treated, with a focus on material recycling and energy recovery. This effort is supported by different management systems, including Extended Producer Responsibility (EPR), free market systems, and tax systems, all designed to ensure environmentally sound disposal of ELTs.
In whichever market, the tyre companies are willing to ensure that their end-of-life tyre arisings are accounted for and dealt with in an environmentally sound way. The producer is responsible for ensuring that his products have a suitable recycling and recovery route.
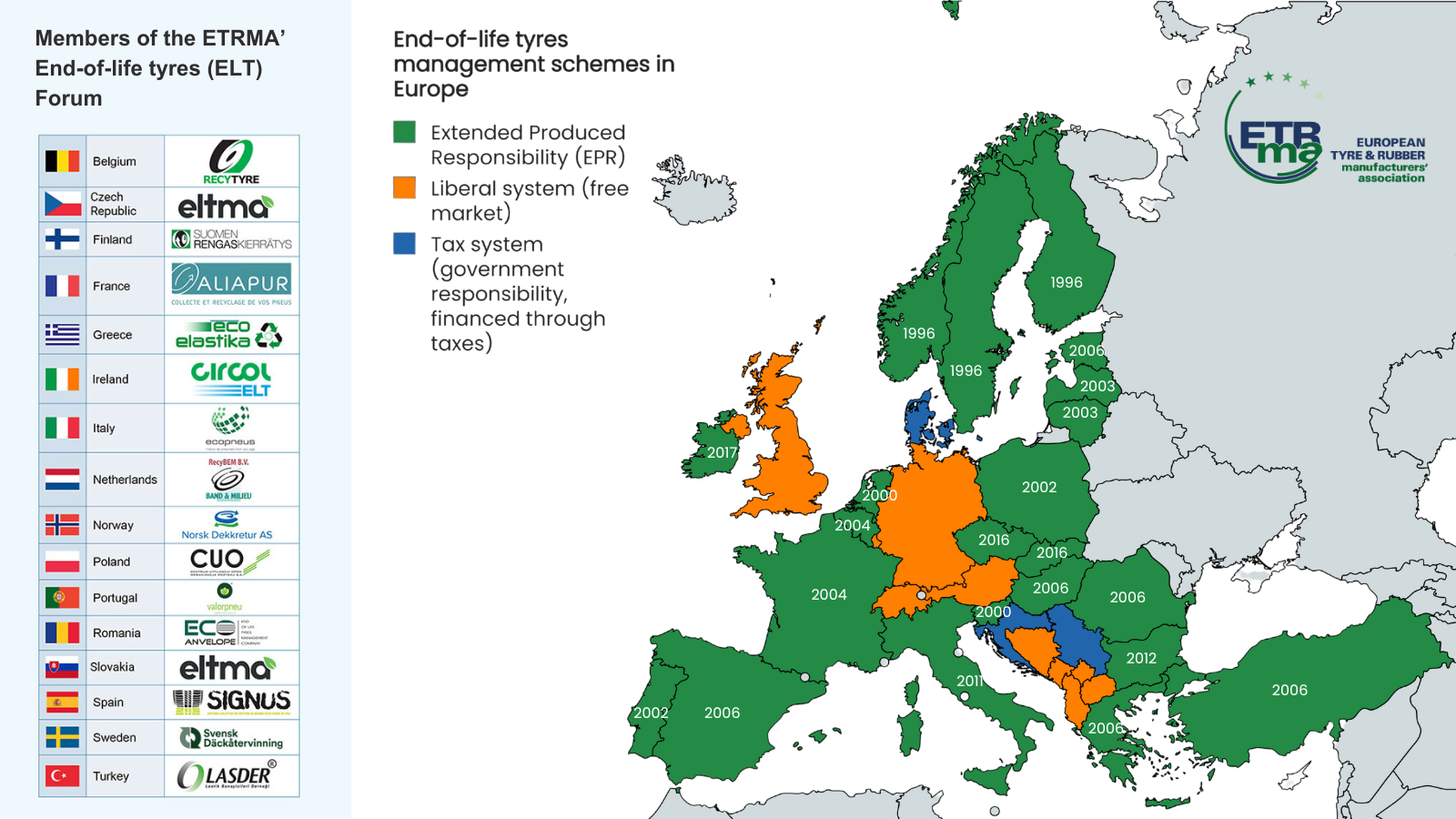
Pyrolysis & Chemical Recycling: Unlocking New Value from ELTs
Pyrolysis technology breaks down tyres into gas, oil, and recovered carbon black (rCB), offering a low-carbon alternative to virgin petrochemical materials.
- End of Waste Criteria: Development of criteria for materials derived from ELTs, including recovered Carbon Black (rCB), to enhance their market potential and ensure quality and safety.
- ETRMA advocates for pyrolysis to be recognised as a recycling process, driving investment in innovative tyre recycling technologies.
Recycling Applications
Secondary raw materials from end-of-life tyres (ELTs) are valuable resources for industries such as construction, automotive, and cement. The European tyre and recycling industries are dedicated to enhancing the value of these materials.
Recycling of ELT-derived Rubber granules and powder
- Process: Shredding ELTs and removing steel and fabric components.
- Applications: Rubber granules are used in products like wheels for caddies, dustbins, wheelbarrows, lawnmowers, urban furniture, signposts, playground flooring, athletic tracks, shock-absorbing mats for schools and stables, paving blocks or tiles, and roofing materials.
ELT-derived rubber powder for rubber modified asphalt
- Benefits: Utilises rubber’s elasticity and noise-absorbing characteristics, increasing road surface lifespan, reducing noise pollution, and enhancing safety in wet conditions.
- Current Use: Limited to a few hundred kilometers of roads.
Use of ELTs in steel mills
- Application: Shredded tyres serve as substitutes for anthracite and scrap metal in electric arc furnaces.
- Benefits: Positive environmental impact on dust and gaseous effluents, utilizing both carbon and steel content of tyres.
Emerging recovery routes: Pyrolysis/Thermolysis
- Technologies: Pyrolysis, thermolysis, and gasification.
- Process: Thermal decomposition of tyres into gas, oil, and char.
Recycling of ELTs in civil engineering applications
- Whole Tyres: Used in projects like coastal protection, erosion barriers, artificial reefs, breakwaters, avalanche shelters, slope stabilization, road embankments, landfill construction, sound barriers, and insulation.
- Shredded Tyres (Tyre Derived Aggregate – TDA): Used as foundation for roads and railways, drainage material, landfill construction, subgrade fill and embankments, backfill for walls and bridges, and subgrade insulation for roads.
- Advantages of TDA: 30-50% lighter, 10 times better drainage than well-graded soil, and 8 times better insulation than gravel.
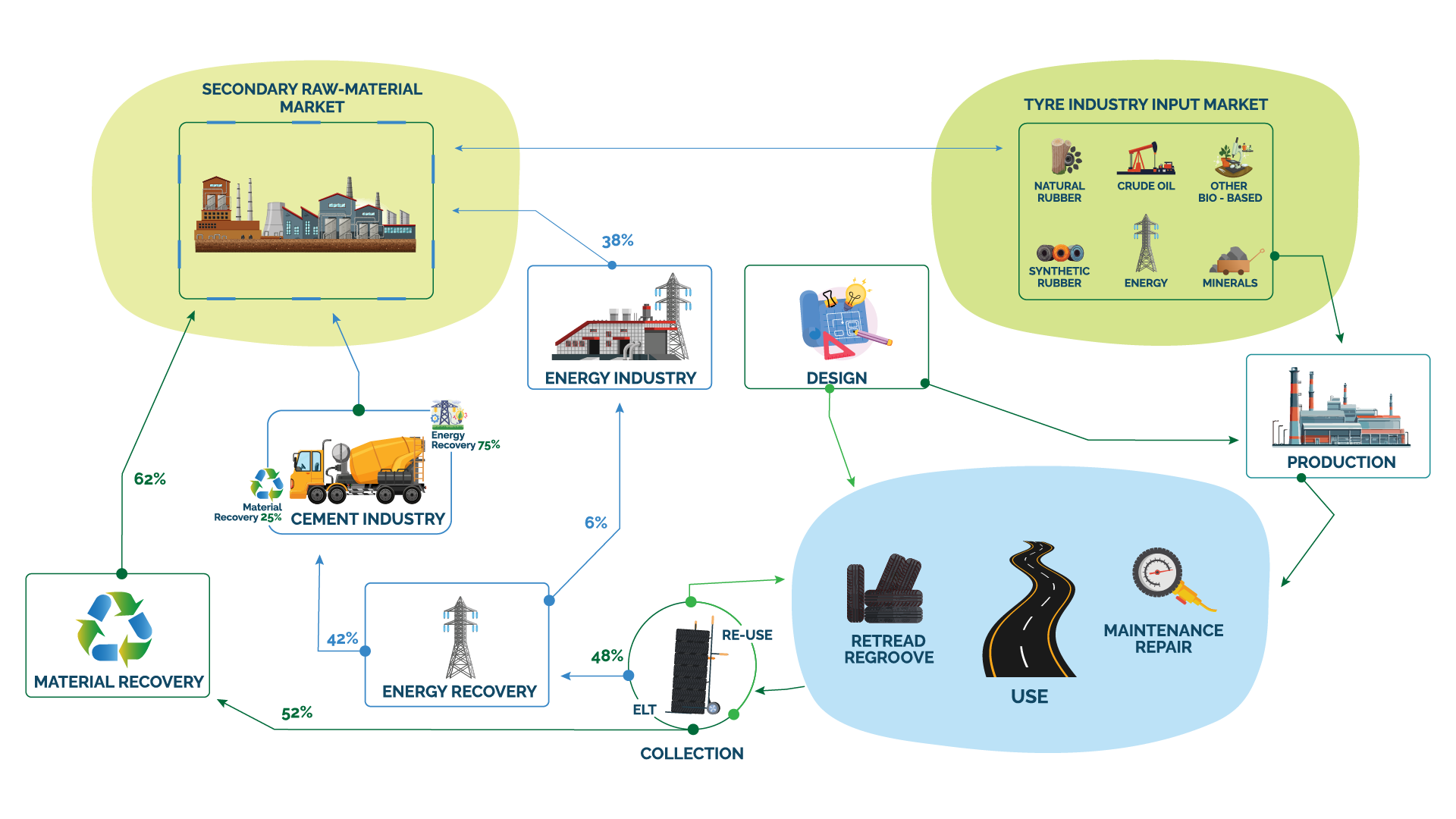